9 Tips For A Successful Warehouse Relocation
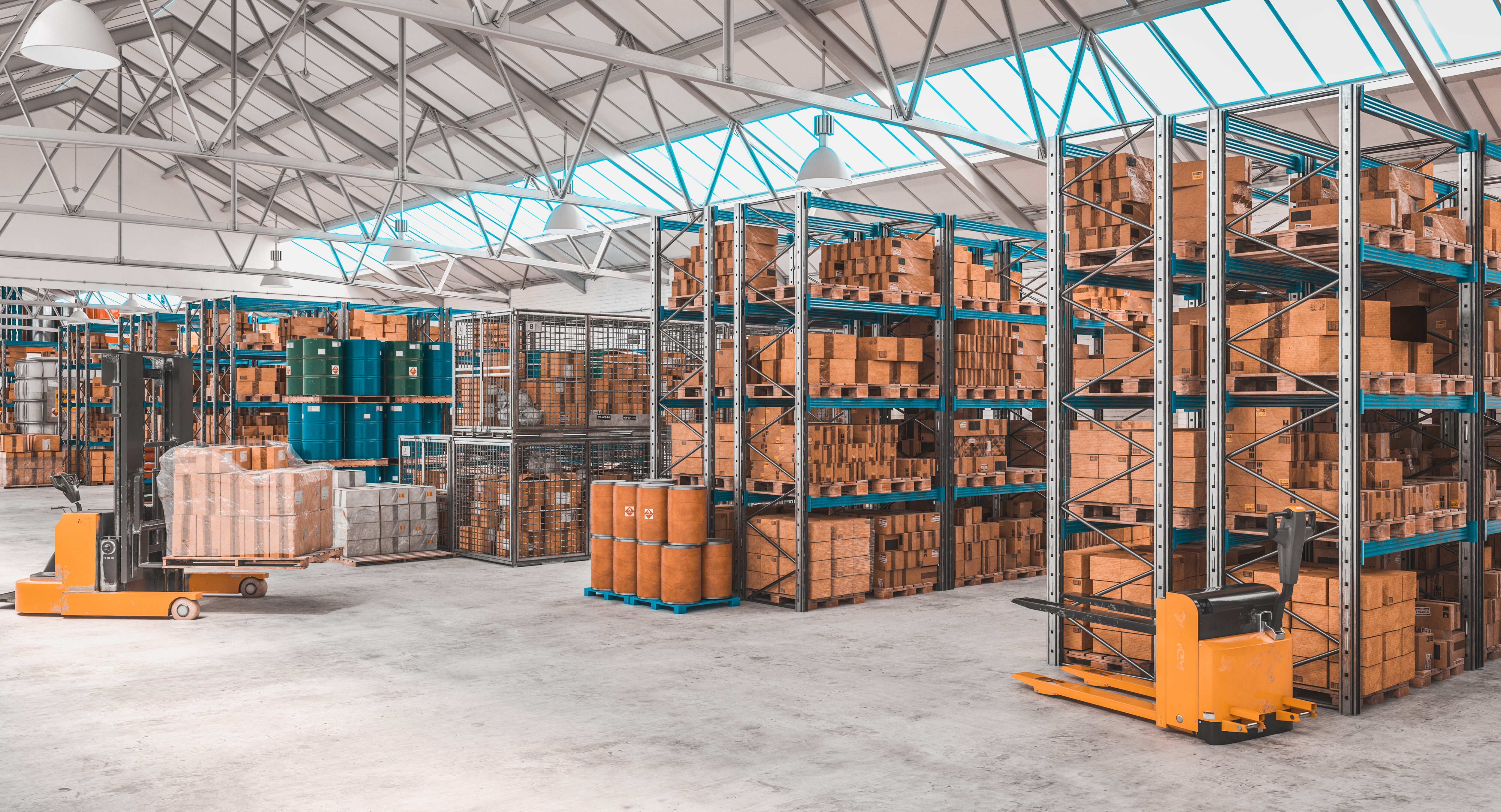
Warehouse relocation can seem like a mammoth task. The logistics, the planning, the coordination, not to mention the risks to business operations —there’s a lot to think about. But with thoughtful preparation and strategy, moving your warehouse doesn’t have to be overwhelming, and you can reduce the risk. Below are nine practical steps to guide your transition and ensure everything goes off without a hitch.
1. Define and Communicate the Objectives
Along the way, warehouse relocations will require many decisions. Clearly defined objectives must be communicated to all stakeholders to help everyone involved stay on the right path. There may be multiple reasons for new warehouse space. These may include expanding to meet increased demand, better technology resources, improving logistics locations, etc. Knowing why the new warehouse space is needed will help everyone stay aligned.
2. Start with a Clear Plan
Any successful move requires a solid plan. This involves setting a timeline, identifying tasks, and assigning responsibilities. Your plan should cover every detail, from inventory relocation to IT setup. Each part of the plan should be developed with the help of the relevant stakeholders. A roadmap ensures everyone is aligned and equipped to handle the tasks.
3. Evaluate the New Location
Ensure the new warehouse meets your business’s needs and aligns with your objectives. Evaluate its size, layout, and accessibility. Verify that it complies with zoning laws and safety regulations. A thorough evaluation helps to prevent future headaches and assures that the new warehouse supports your operations efficiently.
4. Equipment Inventory & Planning is Key
Conduct a complete survey of your warehouse equipment, creating three categories: 1) What will be transferred to the new location? Racks, IT, loaders, etc. 2) Equipment in transition. If overlapping operations, coordinate the equipment transition to ensure continued operations to serve customers. 3) Unneeded Equipment. Arrange for the sale, recycling, or environmentally friendly disposal of equipment that will not be moved to the new location.
5. Invest in Technology
Consider upgrades to your warehouse management software. Depending on the objectives for the new warehouse, a tech review may be in order. If replacing technology rather than upgrading, carefully plan data and process migration.
6. Prioritize Communication
Keeping all stakeholders in the loop is crucial. Regular updates and clear information prevent misunderstandings and setbacks. Establish open lines of communication between employees, suppliers, and partners to ensure everyone is on the same page. Consider regular check-ins throughout the transition.
7. Develop a Transition Team
Select a team dedicated to overseeing the move. Assign distinct roles for each team member, like logistics, equipment setup, and inventory tracking. A specialized team ensures that responsibilities are appropriately managed and that the transition is smooth.
8. Prepare for the Unforeseen
No move goes perfectly, so prepare for unexpected challenges. Whether it’s a delay in transportation or a sudden staffing shortage, contingency plans can make the difference between a smooth transition and a complete disaster.
9. Dial Back Operations Temporarily
Consider scaling down operations close to the move for a smoother process. Inform clients and customers about any potential disruptions well in advance. Slowing operations gives your team the breathing room to focus on relocation tasks effectively.
Your Business, Ready to Conquer New Grounds
Relocating a warehouse doesn’t have to spell chaos for your business. By planning meticulously and communicating regularly, your team can manage a smooth and successful warehouse migration.
Need help planning and executing a warehouse migration? Contact us for a free evaluation.